The Ultimate Guide to Screen Printing: A Colourful Journey for Beginners and Enthusiasts
Screen printing is an intricate art form that has been used for centuries, and yet it remains a vibrant and versatile method. From printing bold, colourful designs on t-shirts to creating intricate art pieces, the possibilities with screen printing are endless. This guide is a literal step-by-step to understanding, starting, and mastering the art of screen printing, whether you're an aspiring artist or a business owner looking to expand your craft.
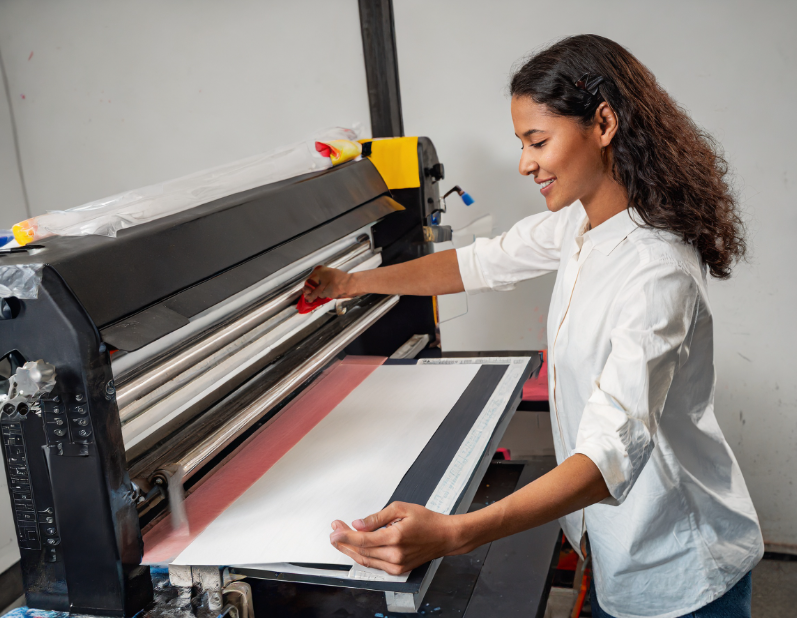
The Art of Screen Printing
To start off, we should appreciate the roots of screen printing. The technique is believed to have originated in China during the Song Dynasty (960–1279 AD) and made its way to Western Europe in the late 18th century. Initially, it was used for items such as wallpaper and luxury fabrics. Today, it’s burgeoned into a method essential across numerous industries, from fashion to signage.
Why Screen Printing?
What sets screen printing apart from other print-making methods is its ability to produce vibrant, long-lasting designs on virtually any surface. Its level of detail, durability, and the variety of materials it can be used on make it a popular choice for artists and designers. Whether you're printing on a small scale for personal projects or mass-producing designs for a business, screen printing offers consistency and quality.
Screen Printing Basics
Screen printing involves creating a stencil on a mesh screen, usually made of polyester or other fine materials, by blocking out areas not intended for ink application. The stencil is then placed over the material to be printed, and ink is spread across the screen. The ink passes through the open spaces of the stencil and onto the material below.
How Screen Printing Works
Screen printing can seem daunting at first, with its various stages and need for precision. However, broken down into steps, it is an understandable and enjoyable process for many.
Step 1: Design Your Stencil
The first step is designing your artwork; this is where creativity meets strategy. Remember, any part of the design you want to print must be "held" by the stencil, while any part you don't want to print should be free. This can either be done with software for intricate designs or by hand, for a more organic shape.
Step 2: Prepare Your Screen
The mesh screen is stretched over a frame, usually made of wood or aluminium. The screen is coated with a light-sensitive emulsion that, when dried, makes the screen impermeable. Your design can be transferred to the screen in two ways: either using a photo emulsion process, where the screen is covered and exposed to light, or by applying a block-out material manually in the form of a cut stencil.
Step 3: Prepare Your Workspace
This might mean setting up a dedicated area in your studio or home, ensuring it's well-ventilated, and all surfaces are covered to protect from ink spills.
Step 4: Apply the Ink
Place your prepared screen over the printing surface and apply ink to the top of the screen. Use a squeegee to draw the ink across the design, forcing it through the mesh and onto the surface below.
Step 5: Cure the Print
For fabric prints, you usually need to heat-set the ink to ensure it won't wash out. For paper and other materials, the method of setting will vary.
Remember, patience and practice are key. Screen printing is as much about the touch as it is about tenacity.
Materials and Equipment Needed
To start screen printing, you will need a few key pieces of equipment and materials.
Essential Equipment
-
Screen with a frame
-
Squeegee
-
Light source (if using photo emulsion)
-
Ink
-
Printing surface
-
Exposure unit or the sun
-
Washout booth or screen cleaner
-
Drying rack or area
Choosing the Right Materials
-
Screen Mesh: The mesh count of a screen determines how much ink will pass through. The higher the mesh count, the finer the detail. Beginners often find a 110 mesh count to be a good middle ground.
-
Inks: There are various types of screen printing inks available, including water-based, plastisol, and discharge inks. Each has its properties and best uses. Always choose the ink that matches your fabric or surface type.
-
Printing Surface: This can be anything from t-shirts to posters to cardboard.
-
Squeegee: The right squeegee is essential, particularly one that is a comfortable size for your screen, as it controls the amount of ink applied.
-
Photo emulsion: This is a light-sensitive chemical that allows you to create a screen directly from your design, through a process of exposure to light.
Always ensure you have spare screens, inks, and cleaning materials – preparation beats downtime.
Understanding Screen Printing Ink Wash
When exploring what is screen printing, it's essential to grasp the basics of the screen printing process, especially the inks and washes involved. Unlike digital printing, which directly applies the pigment to the surface, the screen printing methods involve pushing ink through a mesh screen onto the printing board. At the heart of any screen printing press lies the choice of ink, which can significantly affect the final outcome.
Commercial screen printing operations often utilise a variety of inks to achieve different effects, from standard water-based inks suitable for soft fine art textures to plastisol inks used for creating vibrant and durable designs. Before one can begin the screen printing process step of applying ink, however, preparing the screen is crucial. This involves coating the mesh screen with a photosensitive emulsion, then placing a transparent acetate film with the desired design on the screen and exposing it to light. The areas of the screen protected by the design on the film do not harden and can be washed away, leaving a precise stencil of the image.
The choice between silk screen printing and more modern methods largely depends on the project's nature and the desired result. Silk screens, traditionally made from actual silk, offer a superior quality and feel, making them ideal for fine art and high-end commercial printing tasks. In contrast, synthetic screens are more common in day-to-day commercial screen printing tasks.
Proper ink wash is also a crucial consideration in maintaining the longevity and effectiveness of the screen printing press and screens. After completing a print run, thoroughly cleaning the screens with an appropriate ink wash solution ensures they remain in good condition for future use. This not only extends the life of the printing equipment but also ensures consistent quality across print jobs.
The Art of Design Preparation
Creating and preparing designs is a crucial skill for any screen printer.
Prepping in Digital Spaces
Digital designs offer impeccable precision. Create your design in software, remembering that it will need to be translated into a single colour.
Hand-Crafted Designs
Sometimes, a hand-drawn design can be scanned and then printed onto transparent film to be used in the exposure process.
Consideration for Screen and Ink
Remember that each design will require a separate screen. Additionally, ink thickness and texture can change the end result.
Printing on Different Surfaces
The versatility of screen printing is what sets it apart. Here are some tips for different materials.
Fabric Printing
For fabrics, prepare them by ensuring they are clean, and optionally, pre-stretched to prevent movement.
Paper Printing
For paper, ensure it's flat and secured and move the squeegee slowly for best results.
Printing on Other Materials
From wood to metal to even glass, screen printing can add a personal touch to almost anything. Adapt your process by adjusting your technique and inks.
Tips for Small Business Owners
Starting a screen printing business can be challenging, but immensely rewarding.
The Business Side
Understand your market, pricing, and marketing. You're selling a story as much as a product.
Sourcing Materials
Find reliable suppliers – your business's consistency will be based on their reliability.
Quality Control
Ensure you have established methods for quality checks and have policies for replacing defective products.
Legal Considerations
Understand copyright law as you'll often be printing designs created by others.
Scaling Up
Invest in automation and technology as your business grows.
Community Spotlight
Lastly, take inspiration from those who have walked the path before you – engage with the screen printing community.
Profiles of Success
Learn from others, understand their challenges and what led to their triumphs.
DIY Enthusiasts
Join online forums or local screen printing clubs. There's always something new to learn.
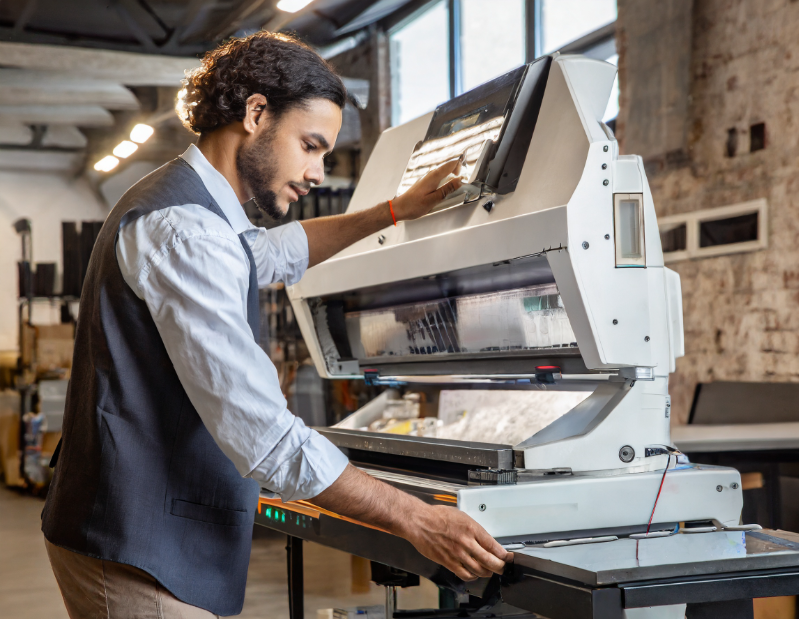
Conclusion and Call to Action
I hope you're as excited about screen printing as I am. It's a medium that bridges the gap between the meticulousness of art and the edginess of design.
Keep Printing
Experiment, fail, learn, and improve. Every print is a step forward.
Share Your Creations
Be proud of what you print and share it with the world. Collaboration and community are at the heart of the screen printing world.
Leave a comment